What is the difference between Ultrasonic Welding and Vibration Friction Welding
Ultrasonic welding and vibratory friction welding are both processes that use vibrational energy to weld plastic components, so they are often confused. However, the two welding method processes are still different, let’s take a look at the differences between these two welding processes and how you can use them to your advantage.
Vibration welding plastics: Both ultrasonic welding and vibration friction welding use vibration to create friction and generate heat to weld plastics.
Ultrasonic welding is a welding technique that uses high-frequency ultrasonic vibrations to heat and fuse two metal materials together. Vibratory friction welding is by applying a vibrating force at the metal junction, and the friction generates heat so that the two metal materials are fused under high-temperature conditions.
Vibration Friction Welding

Principle: Friction welding uses a mechanical brake to generate friction heat between two metal parts, causing it to be locally heated to the welding temperature, and then applying pressure to connect the two metal workpieces.
Process: High temperature is generated between two workpieces through rotation, vibration, or friction. When the appropriate welding temperature is reached, the heating is stopped and pressure is applied to fuse the metals.
Advantages: It can be used for welding different materials with fast speed, high-quality welding head, low cost, and no need for additional welding materials.
Application: Suitable for automotive manufacturing, aerospace, railways pipelines, etc., used to join components of different metals.
2. Ultrasonic Welding
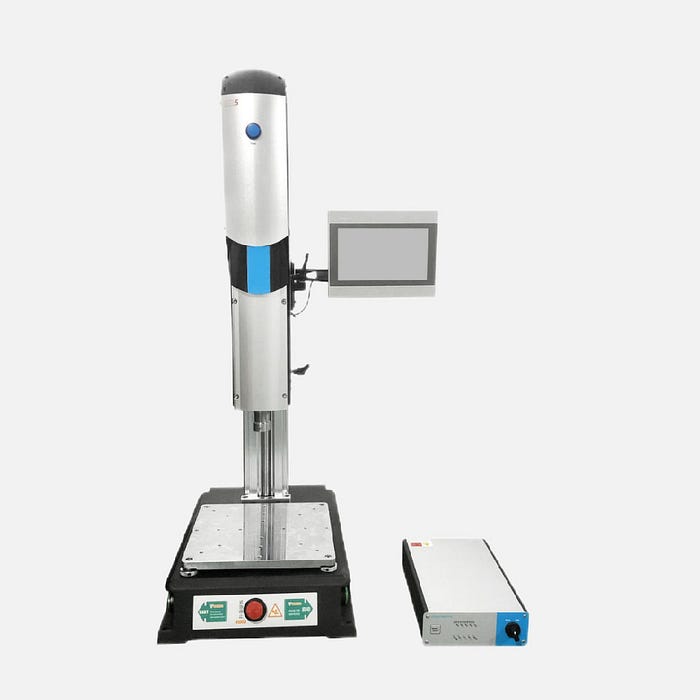
Principle: Ultrasonic welding uses ultrasonic vibrations to cause surface friction between two workpieces to generate heat, causing the materials to partially melt and join under pressure.
Process: Ultrasonic waves are transmitted to the surface of the workpiece through the welding head, causing material vibration and heat, and then applying pressure to connect the workpieces.
Advantages: It can complete welding in a short time, the welding head quality is good, the requirements on the metal surface are low, and no additional welding materials are needed.
Applications: Thermoplastic plastics, electronic devices, medical equipment, batteries, wire connections, and other fields.
These two welding methods have the advantages of fast, efficient, and energy-saving, and are suitable for many different kinds of metals or materials. The choice of which method to use usually depends on factors such as the type of material, the required welding quality, the shape of the workpiece, and the welding conditions.